Smart robots to make smaller chips

A robotic arm in a factory that repeatedly performs the same movement: that’s a thing of the past, argues Ming Cao, Professor of Networks and Robotics and Director of the Jantina Tammes School of Digital Society, Technology and AI. ‘We’re moving towards smart industry, with robotic arms that are able to make decisions.’ Various researchers at the University of Groningen are collaborating with high-tech companies such as chip manufacturer ASML to make production processes more autonomous.
FSE Science Newsroom | Charlotte Vlek
‘Manufacturing a chip is a fully automated process,’ Cao explains, ‘there is very little human interaction involved.’ But our electronic devices can do increasingly more while becoming smaller and smaller, which means that chip production has to become even more accurate at a tiny scale. And that means that the machines that produce chips need to be finetuned to compensate for small changes in temperature or humidity in the factory. Cao: ‘Such a thing is beyond human capabilities. But a sensor is able to pick up miniscule changes instantly.’
Obtaining a flat silicon wafer
For example, consider the material that forms the basis of a chip: silicon. A flat strip of silicon, called a silicon wafer, is placed under a laser beam that transfers layers of interconnected patterns onto the wafer at a nanoscale. It’s of great importance that the silicon wafer lies completely flat, because as soon as the laser hits the surface at an angle, the laser bundle goes out of focus, causing inaccuracies.
That’s why Bayu Jayawardhana, Professor of Mechatronics and Control of Nonlinear Systems, and Mónica Acuautla Meneses, associate professor of Engineering Materials for Mechatronic Systems, have teamed up with chip manufacturer ASML to develop a deformable wafer table on which the silicon wafer can lie completely flat. To do this, they use a piezo material that expands at a specific location when a voltage is applied to it. This allows each part of the wafer table to be adjusted as required.
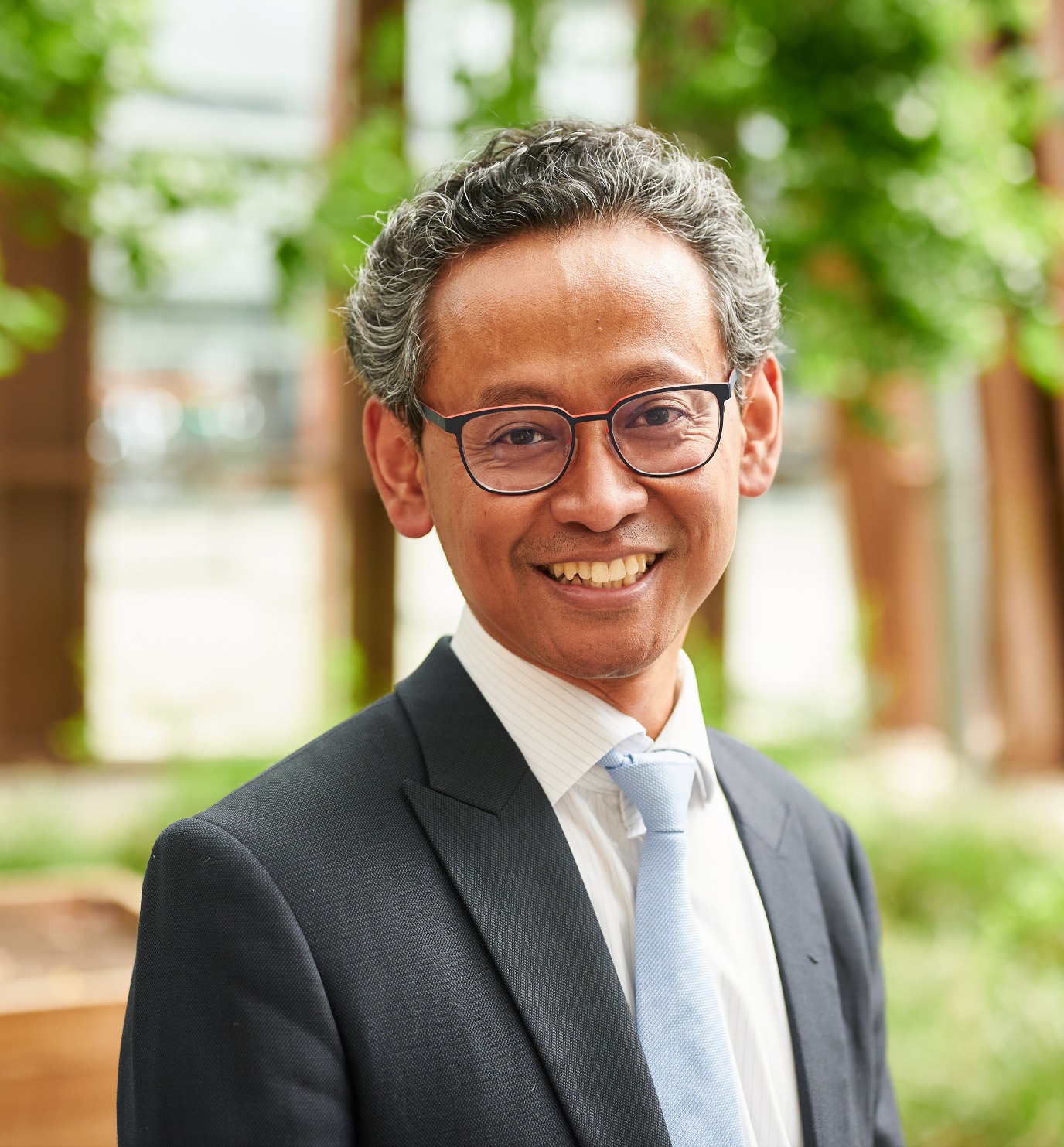
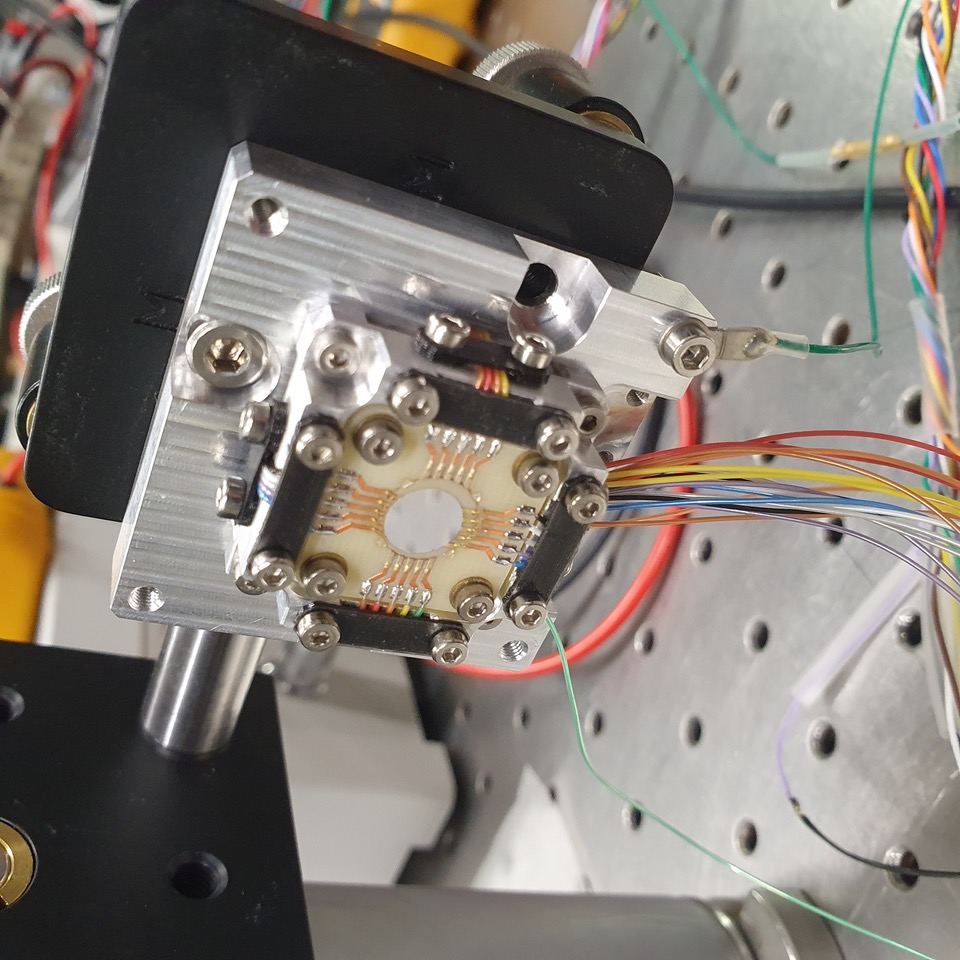
A deformable wafer table
The idea actually came from an earlier project undertaken by UG researchers Jayawardhana and Acuautla together with instrument scientists of SRON, for which they developed a deformable mirror for the observation of exoplanets. Getting lightwaves from space to hit the mirror just right was important to get the clearest signal – similar to the laser at ASML that needs to hit the silicon wafer accurately, though at a much smaller scale.
To create a deformable surface, they use a piezo material. Wires are connected to the material to create a grid of ‘pixels’, so that each pixel can be adjusted to make the material in that spot expand to the desired height. Jayawardhana is working on the calculations to control the current that goes through each pixel. ‘The main challenge was the huge number of wires that would be needed,’ he explains. For a piece of one hundred by one hundred pixels, this would amount to 20,000 wires: two per pixel, so that each pixel could be controlled individually.
To reduce the number of wires, Jayawardhana uses a memory effect in the piezo-material, which means that each pixel can be set one after the other. This way, far fewer wires are needed – only 200. ‘For each pixel, we measure how much voltage is needed to reach the required height, we measure the actual effect to further finetune. This way, we can set all pixels one after the other, until the right surface shape is achieved.’
Getting all parts to work together
An engineer at ASML may know from experience that a particular part of machine will only function well under certain circumstances, but we bring automation into the design process
The wafer table is just one part of a machine that makes the chip. Such an element might be developed by an expert on piezoelectric materials, whereas another expert might provide the required control algorithms. But how do you ensure that all these different experts develop elements that actually contribute the right things to the system?
Bart Besselink, associate professor in Systems and Control, is working on mathematical methods that can specify the elements of such complex systems. ‘These could be complex systems such as machines in a chip factory, but also a self-driving car, or a smart energy system,’ Besselink explains. ‘The core idea is to formulate in a mathematically precise way what specifications each element must meet.’
‘An engineer at ASML may know from experience that a particular part of machine will only function well under certain circumstances, but we bring automation into the design process.’ This facilitates discussion between various design teams, and they may even be able to negotiate which requirements are absolutely necessary, and which requirements can be relaxed.
Specifications for industrial practice
Autonomous systems combine physical hardware with sensors that take measurements, actuators that can initiate actions, and a software layer to control everything. Each element of such a system is developed by a domain expert, such as a software developer for the software, and a technician for the sensors.
To ensure that each element contributes to the larger system as it should, they need to satisfy certain specifications. ‘Often, these are dynamic properties,’ Besselink explains, ‘something that changes over time’, for example temperature changes in a chip factory, or the speed of an autonomous car.
By capturing these dynamic specifications in formulas, the design of such a system can be accurately worked out, which in turn guarantees the desired system behaviour. The next step for Besselink is to bring his mathematical design help one step closer to industrial practice. To this end, he will soon work together with various companies that will work with these design tools.
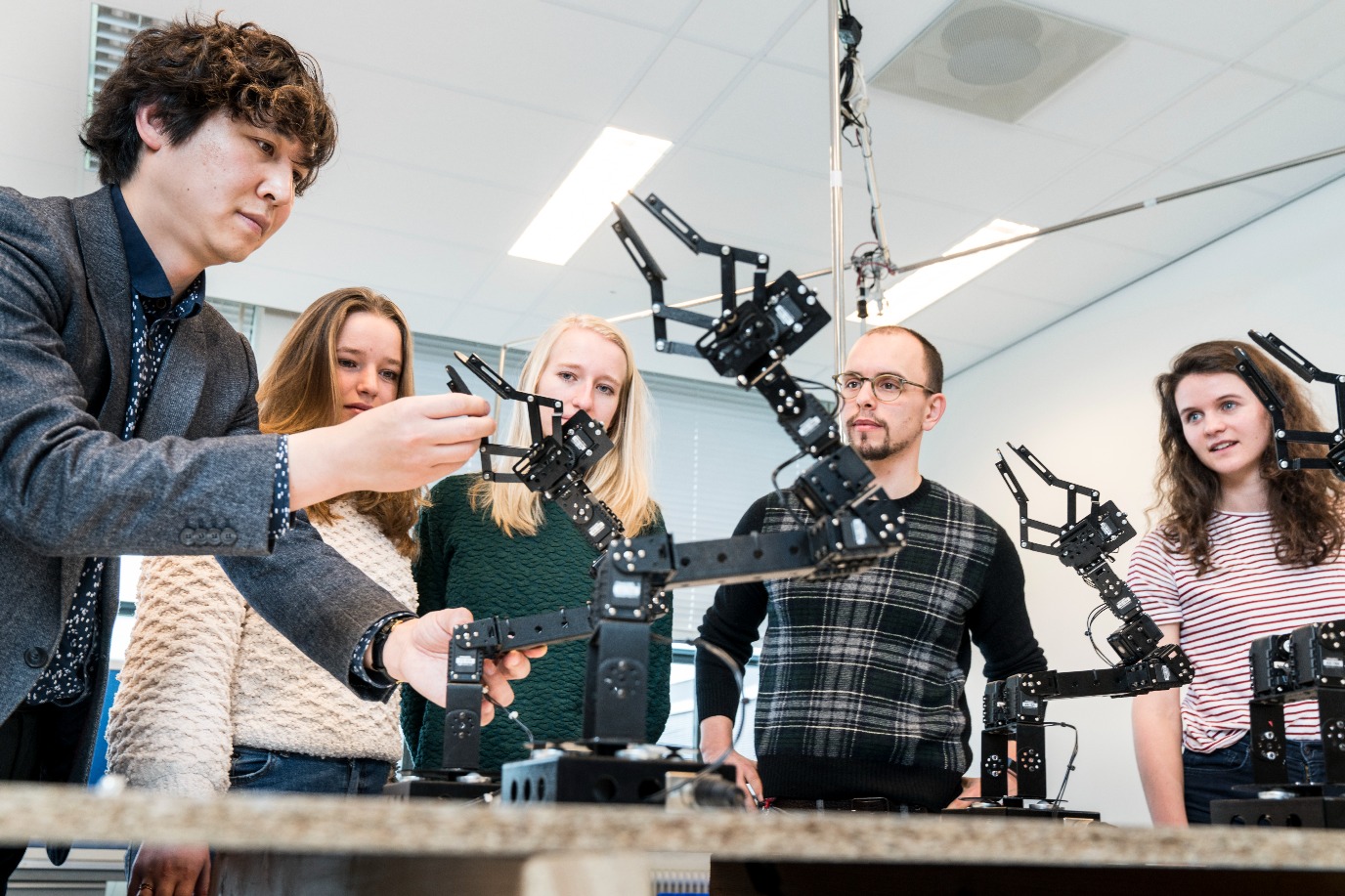
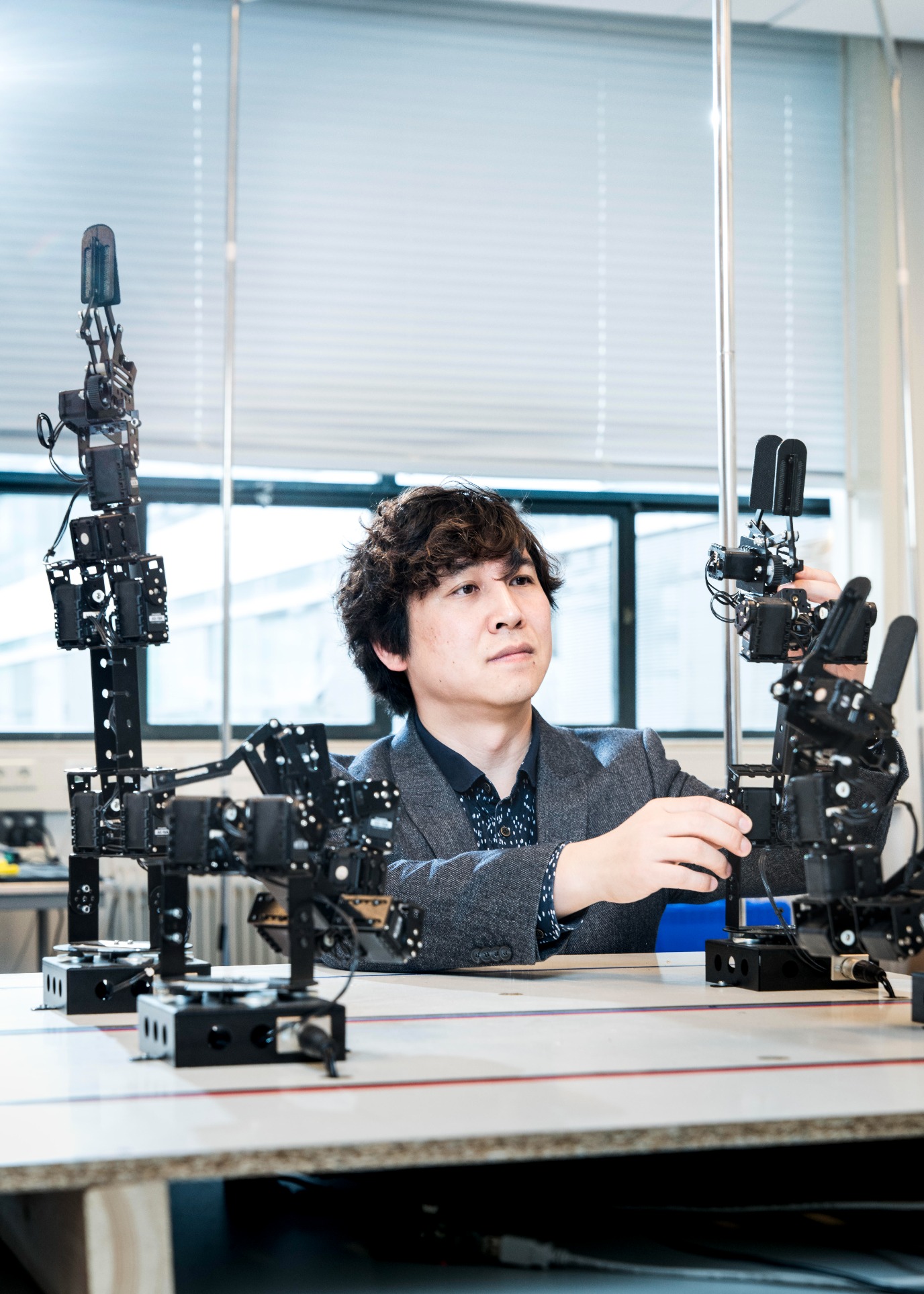
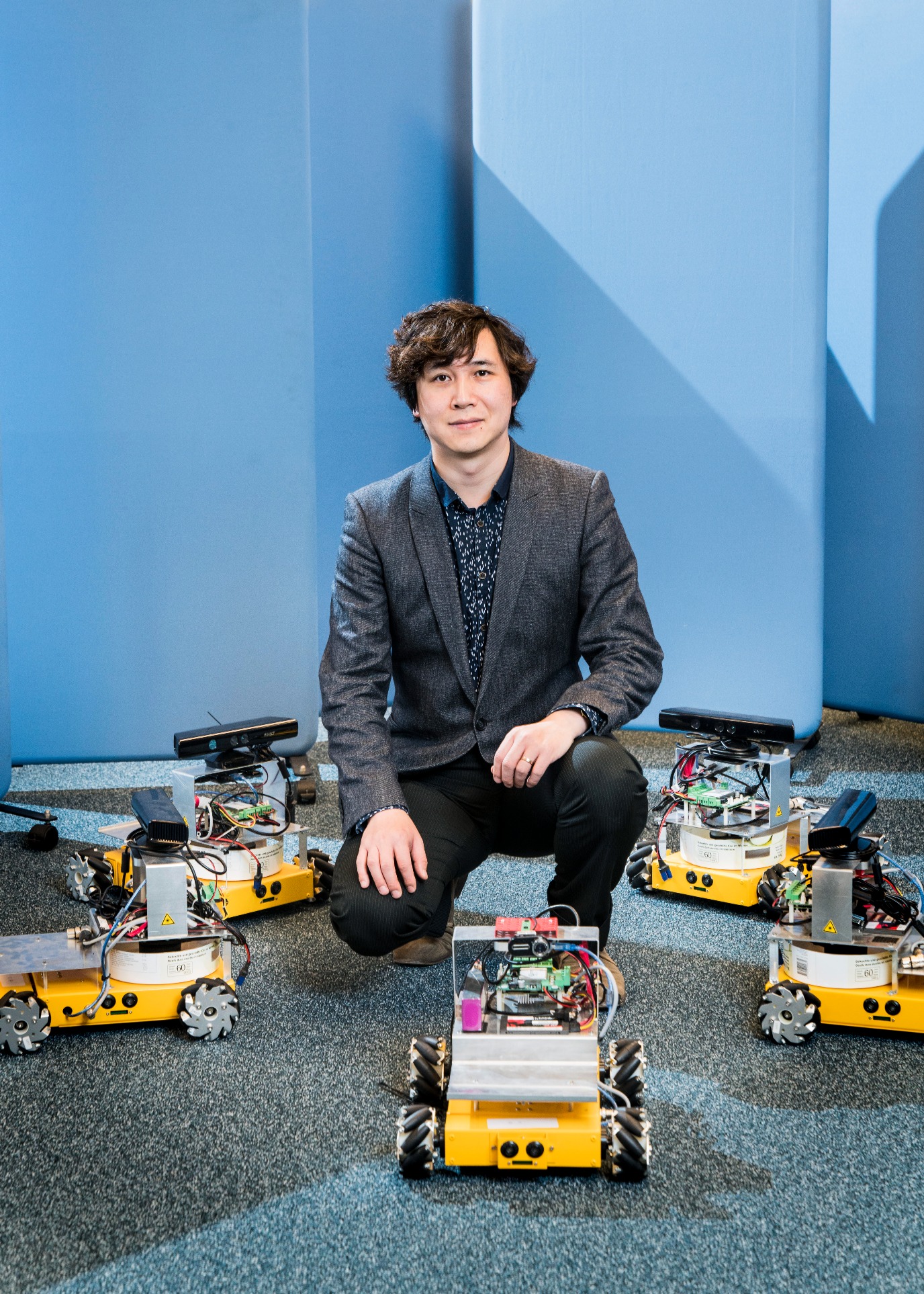
Collaborative robots
It’s just like with humans. There needs to be mutual trust to be able to collaborate.
Ming Cao is also exploring how multiple elements can work together. ‘For example, consider robots that assemble a product: one gathers the necessary components, while the other puts them together. In such a case, it would be helpful if they could exchange information: if the first robot already knows the weight of a component, it could then share this information with the next robot.’
‘But it’s just like with humans,’ Cao adds: ‘there needs to be mutual trust to be able to collaborate.’ Because what if a neighbouring robot’s information does not match their own measurements? That is when Cao’s robots will start negotiating with each other, and they will do so in milliseconds: ‘These are complex situations that need to be evaluated in a short time, with little room for error. Just like multiple robotic arms that work together in a factory.’
Collaborating robots under water and in the shaver factory
Some work cannot be done by humans, such as the maintenance of offshore wind farms. Cao is working with Fugro Innovation & Technology to develop underwater robots and surface vehicles for such wind farms at sea. These robots would be able to assess whether a wind turbine is still functioning, and if there are any cracks, for example. Cao: ‘These robots then need to make decisions, such as: which one of us will inspect this crack – the one closest by, or the one with the highest battery level?’
Cao is also working with Philips Drachten to automate the production of shavers. The goal is not to produce the same shaver over and over again, but to have the same robotic arms assemble different types of shavers. Cao enjoys the research behind such a question: ‘It’s a nice research challenge!’
High on the autonomy ladder
Cao, Jayawardhana, and Besselink are all working on autonomous systems in industrial applications. This way, they want to bring innovation to Dutch industry. They will soon do this through a new ecosystem in the north of the Netherlands: Infinitech, which brings together questions from industry and solutions from academia.
Jayawardhana gives an example: ‘Imagine the various levels of autonomy as a ladder. A car with cruise control is just one small step on the autonomy ladder, while a self-driving car is at the top of the ladder. We want to take companies as high as possible on this autonomy ladder. There are so many beautiful ideas; the key question is what applications they can be used for.’
In September 2024, the University of Groningen will start the new Engineering Doctorate in Autonomous Systems. Trainees will work at a company as well as at the UG to develop technical solutions for the automation of systems in the high-tech industry.
Read also: 'The chip of the future' (appears next week)
Published on: | 23 July 2024 |
Our computers use an unnecessarily large amount of energy, and we are reaching the limits of our current technology. That is why CogniGron is working on new materials that mimic the way the brain computes, and Professor Tamalika Banerjee will develop chips for energy-efficient computers with her start-up company IMChipN .
Last modified: | 23 July 2024 09.30 a.m. |
More news
-
03 April 2025
IMChip and MimeCure in top 10 of the national Academic Startup Competition
Prof. Tamalika Banerjee’s startup IMChip and Prof. Erik Frijlink and Dr. Luke van der Koog’s startup MimeCure have made it into the top 10 of the national Academic Startup Competition.
-
01 April 2025
NSC’s electoral reform plan may have unwanted consequences
The new voting system, proposed by minister Uitermark, could jeopardize the fundamental principle of proportional representation, says Davide Grossi, Professor of Collective Decision Making and Computation at the University of Groningen
-
01 April 2025
'Diversity leads to better science'
In addition to her biological research on ageing, Hannah Dugdale also studies disparities relating to diversity in science. Thanks to the latter, she is one of the two 2024 laureates of the Athena Award, an NWO prize for successful and inspiring...